Good scheduling is crucial for a successful logistics chain. Doing it well can boost revenue, but doing it poorly can stop your entire operation.
Falling behind on production or missing shipments because of timing issues is a big problem. Logistics scheduling is how you avoid that and keep everything running smoothly.
In this guide, we'll explain why mastering logistics supply-chain scheduling is crucial. We'll also show you simple ways to make the scheduling process smoother. Additionally, you'll discover why last-mile delivery is key to keeping your customers happy.
Jump to the section that interests you most:

Understanding Logistics Scheduling
Logistics scheduling involves selecting specific days and times to transport products or services through the logistics process. It includes planning when specific parts arrive for production. It also involves scheduling the delivery of your packaged product to your customer's doorstep.
The Significance of Logistics Scheduling
Logistics is the start and finish of your entire supply chain. That makes logistics scheduling crucial for your revenue. According to a global survey by Deloitte, more than two-thirds of retail and manufacturing businesses have well-performing supply chains. These businesses experienced an above-average increase in revenue.
Achieving a top-notch logistics chain involves scheduling early and consistently. A widely-used approach is forward scheduling. It requires completing each stage as soon as time and resources permit. When you improve your skills in scheduling time and resources, you deepen your understanding of each logistics step. This enhancement contributes to improved planning abilities.
If you divide 30 minutes for loading trucks, it works. But if there are two larger trucks taking 45 minutes each to load, it might not go smoothly. Starting with the larger trucks means your team starts the day 15 minutes late. They might even encounter traffic or face delivery challenges. In this case, a 15-minute delay can grow to a 2-hour delay by the end of their shift. In logistics, if one part operates inefficiently, it affects every step after it. So, those minor delays tend to build up quickly.
Logistics scheduling helps pinpoint delays. It also allows managers to make corrections where congestion or hold-ups happen. A detailed schedule serves as a roadmap for the success of your entire supply chain.
Ensuring the final delivery mile guarantees customer satisfaction and repeat business
Last-mile delivery is the final step in which goods are physically taken to customers from warehouses. It is a crucial part of logistics because it directly interacts with customers. Even if your procurement and packing are flawless, late deliveries create unhappy customers.
Scheduling resources and time for last-mile delivery is tougher. It is due to retailers like Amazon providing quick and free delivery for various items. Over half of online shoppers expect their products to arrive in 3 hours or less. Customers demand speedy deliveries, and delays can have a big impact on their loyalty. Thus, it's evident that even small businesses must excel in last-mile delivery.
Fortunately, leveraging technology for logistics scheduling can cut last-mile planning time by up to 90%. It not only increases efficiency but also triples capacity.
Actual Outcomes of Scheduling in Logistics
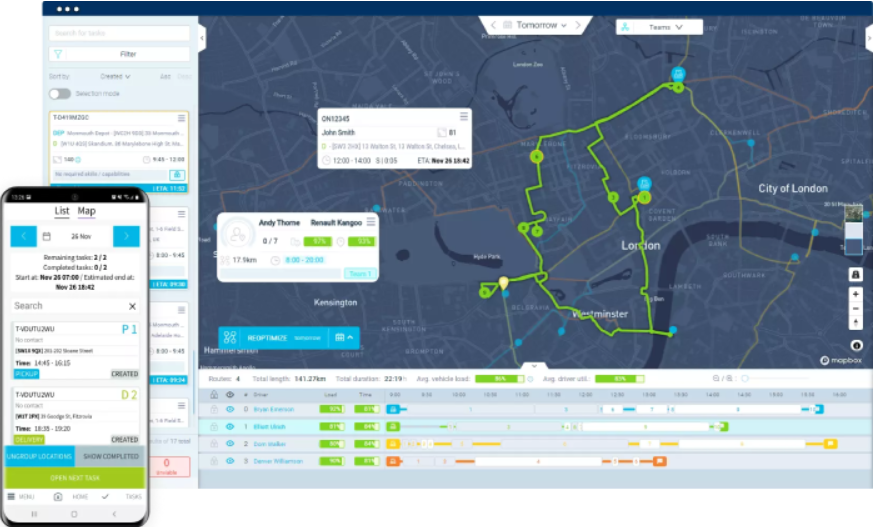
Companies can boost their revenue by streamlining their logistics process, enjoying various benefits. Here are some examples:
Enhanced Risk Management and Scalability
Scaling any part of a logistics chain demands knowing how long each step takes. Logistics scheduling provides precise data for achieving various business goals. That includes ordering supplies or hiring seasonal staff.
Also, the schedule can be a guide to identify cost-cutting opportunities during low demand. Well-planned schedules help managers decide which orders can wait. It allows them to determine whether they can reduce work hours. It also helps to focus on supplies and prevent expiration in unforeseen circumstances.
Reduced Overhead and Minimized Stockouts
A well-crafted schedule ensures each logistics step happens at the right time. That means not too soon, not too late. The balance reduces costs and prevents stockouts, which can lead to losing customers.
Imagine operating a custom graphic T-shirt business. Bulk orders of blank shirts arrive every first Tuesday monthly. With a small warehouse and limited space, planning is crucial. April sees increased demand for women’s shirts (Mother’s Day). Also, late May and June see a surge in demand for men’s shirts (Father’s Day).
With effective logistics scheduling, you can adapt T-shirt supply deliveries. It will help you meet demand without requiring extra warehouse space. For instance, you can increase April's order for women's shirts and cancel the May order. Such straightforward scheduling can save warehouse space. It can also prevent shirt shortages during peak seasonal demand.
Increased Time and Reduced Expenses
Good scheduling helps you plan ahead, avoiding last-minute chaos. Ordering supplies beforehand saves money by avoiding rushed orders with higher costs. Effective last-mile logistics planning cuts down on unnecessary trips. It, in turn, saves fuel and vehicle maintenance expenses.
Effective scheduling, by nature, requires less time. That allows management teams to have more capacity to concentrate on logistics strategy and higher-level planning.
Increased Timely Deliveries and Satisfied Customers
We addressed the risk of losing customers and revenue with poor last-mile delivery. The good news is that when last-mile delivery is well-planned, there are significant benefits. Effective scheduling ensures more on-time deliveries, leading to happier customers and positive reviews.
For successful last-mile delivery scheduling, managers should understand how long it takes to drive between locations. Also, they need to count how long it takes a driver to stop and deliver a package. When each time window is understood and scheduled accurately, the entire operation runs smoothly. That makes on-time deliveries easier.
Scheduling driver breaks strategically minimizes route impact. Balancing workloads across the fleet becomes easier. This simplification aids in creating schedules for on-time deliveries. Satisfied customers are more likely to return.
Enhancing Logistics Scheduling Through Appropriate Software
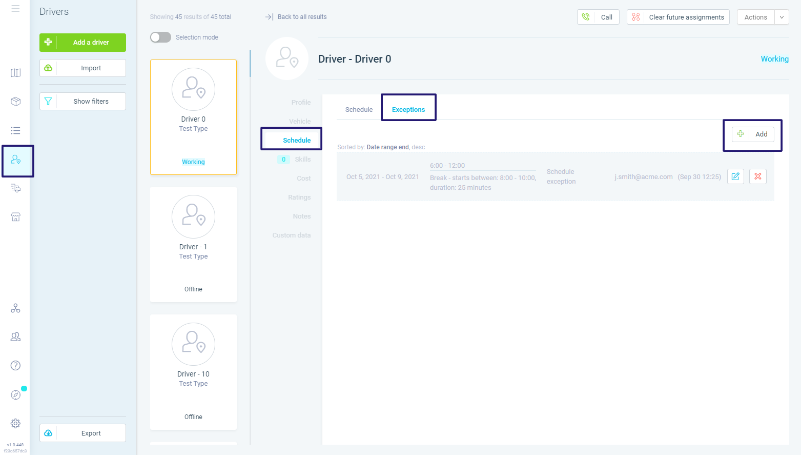
Managing logistics scheduling deals with many numbers and moving parts. Often, problems arise from slow manual calculations. That can be easily resolved by adopting technology. Utilizing appropriate software for each stage ensures synchronization throughout your supply chain. Thus, it saves employees significant time. Now, let's explore essential logistics points and how technology simplifies these processes.
A spend-management software
Effective spend-management software is crucial for saving time and money. Streamlining the supply ordering process is vital to prevent logistics delays. A smooth expense approval system is essential for timely procurement. Inventory management software with vendor management facilitates quick purchase order creation. Real-time budget tracking ensures a clear overview of expenses. Preapproved spending limits cut lengthy approval processes and maintain efficient logistics flow.
Inventory management
Efficient inventory management is crucial for businesses to track stock levels and streamline operations. Without proper systems, tracking product quantities becomes challenging. This can lead to stockouts or excess inventory. This can result in increased warehouse costs.
A well-implemented inventory management system categorizes and tracks products based on various criteria. This replaces manual stock counting, providing real-time information through digital platforms.
Having a clear overview of inventory levels empowers decision-makers to make informed choices. They can adjust stock levels and optimize warehouse space. This contributes to improved efficiency and cost-effectiveness for the business.
Last-mile delivery
For last-mile logistics scheduling, turn to eLogii. Plan up to five weeks ahead with ease. Schedule numerous optimized routes that have many constraints with just a click. Adjust schedules without effort for unexpected changes or new orders.
You can even schedule orders with quick turnaround times effortlessly and efficiently. Moreover, Ananas utilized eLogii's software to enable customers to independently postpone or change delivery times. This is possible through the user-friendly reschedule functionality. This option exists on the customer portal/tracking page.
With route optimization tools, individual vehicle cargo space can be taken into consideration. It helps to maximize capacity usage and cut return trips for reloading. This feature can enhance delivery efficiency. It is especially helpful during busy holidays with significant order volume increases.

eLogii provides live tracking for your entire field service team, offering real-time visibility. It enables managers to easily identify any deviations from the planned route. The software assists managers in enhancing driver scheduling, appointment scheduling, and future routing. The live tracking feature also ensures customer satisfaction. It allows them to see the package location and receive precise arrival time notifications.
eLogii incorporates user-friendly features for scheduling driver breaks and balancing workloads. In the context of last-mile delivery, eLogii streamlines the entire scheduling process. It offers benefits to your business, customers, and employees.
Reverse logistics
Reverse logistics manages used appliances and product returns, crucial for businesses. Attention to scheduling here saves time and addresses return challenges.
eLogii enhances the efficiency of reverse-logistics scheduling and planning. It easily combines pickup routes with existing delivery routes. That helps to reduce planning time, fuel costs, and driver hours. For product returns, eLogii simplifies restocking and minimizes confusion related to stock level changes.
Depending on your business type and logistics needs, many software and selling platforms, like eLogii, can aid in streamlining logistics scheduling. Integration of your tech stack further simplifies the process, saving you valuable time.
Your Logistics Scheduling Ally
The eLogii team is ready to assist you with comprehensive scheduling, route planning, and leveraging data analytics to enhance your last-mile and reverse logistics. We've supported many businesses in optimizing their logistics processes and boosting revenue.
