Shipping and logistics expenses have been going up consistently since the COVID-19 pandemic began. The trend of high logistics costs continued into the summer of 2023 and is expected to persist in 2024. These rising costs will have a big impact on your business. So, learning about logistics expenses can help you understand and manage them better within your own business. Then you can find ways to lower costs and boost your profits.
What Do Logistics Costs Include?
Shipping logistics costs refer to the expenses involved in handling, managing, and transporting goods. These costs cover everything from acquiring raw materials to utilizing a third-party logistics provider for distribution help.
Understanding 4 Types of Logistics Costs
Within the supply chain, various components contribute to logistics expenses. These costs typically fall into four main categories: warehousing, transportation, labor, and equipment. The specific nature of these costs may vary based on your business and industry.
Managing Inventory Storage Costs
Every business, whether producing in-house or using third-party manufacturing, requires storage for inventory. As your inventory grows, so does the need for space. Yet, finding rental warehouse space is becoming increasingly challenging. That is due to rising costs and limited availability. In 2023, rental renewals in the U.S. reached a record high of $9.72 per square foot. That is driven by the expanding e-commerce sector, which is causing a shortage of warehouses. Purchasing warehouse space outright may seem like an alternative, but it is unlikely to be a more cost-effective solution.
Other Costs Associated with Warehouse Management:
- Insurance
- Utilities
- Security
Transportation and Distribution Costs
Transportation and distribution represent significant logistics expenses for businesses. That is true whether using third-party logistics providers (3PL) such as reverse logistics companies, or managing an in-house team. These costs involve various tasks, including:
- Transporting raw materials to your manufacturing facility
- Moving products from manufacturing to your warehouse
- Delivering packages to customers
Inbound logistics, like transporting goods from the manufacturer to your warehouse, involve cost-effective transportation tasks with large shipments to a central location. But outbound logistics, such as last-mile delivery, tend to be much more costly.
Final Delivery to Customers
"Last mile delivery" is the process of directly delivering products to your customers, which is the last step in distribution. This stage requires a lot of time and resources. This is because drivers need to make many stops to deliver small quantities of products to individual customers. Delays can happen due to security gates or reception desks, each with their own procedures for receiving deliveries, making the process slower. Last mile delivery is the most expensive part of your supply chain, accounting for half of your total shipping costs.
Labor Costs
The cost of your staff who produce, manage, and transport your products can vary widely. How much you spend depends on where your staff works and the average pay rate in that area. For instance, if you operate in Texas, you might pay delivery drivers around $42 per hour, which is the local average. Yet, in New York City, where the average pay is closer to $55 per hour, you'll need to offer slightly higher wages to compete. Different team members will also earn different wages based on their job titles and experience levels.
Common Positions Needed in Logistics:
- Warehouse staff responsible for receiving new inventory and preparing packages for delivery
- Delivery drivers tasked with transporting materials and products
- Managers overseeing employees, warehouse operations, and logistics processes
- Administrators managing human resources, including payroll processing and hiring new employees
Equipment and Supplies in Logistics
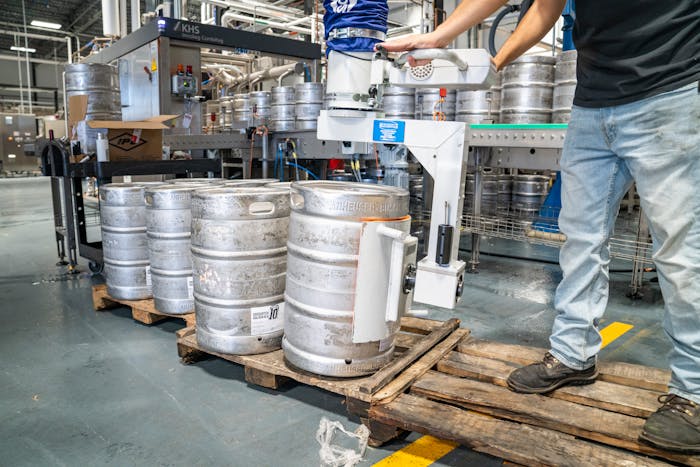
The tools and supplies essential for keeping your operations efficient also affect your costs. This category covers a range of items required across your supply chain. If you manufacture your products, all manufacturing tools fall under this expense category. Within your warehouse, necessary equipment may include:
- Shelving
- Pallets
- Forklifts
- Boxes
- Tape
- Inventory software
Let's say you manage delivery and transportation in-house. In that case, your equipment expenses will cover maps, routing software, driver uniforms, and delivery vehicles. Additionally, there are ongoing expenses such as fuel, insurance, and vehicle maintenance.
Measuring Logistics Costs
To measure your logistics costs effectively, start by choosing a timeframe for assessment. Monthly evaluations can help ensure your costs align with your budget. For a broader perspective, assess these metrics quarterly and annually to inform comprehensive business reports.
Once you've established your timeframe, begin measuring costs across four categories: warehousing, transportation, labor, and equipment.
Steps to Measure Your Costs:
- Identify all your expenses and list them as line items.
- Record the precise cost for each expense.
- Sum up the line items within each category.
- Total the expenses for each category.
Following these steps will provide a clear breakdown of your expenses in each category. You can then add the totals across categories to determine your overall costs.
For instance, if you pay $1,000 monthly for warehouse rent and $600 for utilities, your warehousing costs for that month would be $1,600. Additionally, you spent $1,500 on delivery drivers and $2,000 on warehouse staff, totaling $3,500 for labor.
Yet, these figures only cover half of your total monthly logistics costs. To calculate the full costs, include transportation and equipment expenses.
Assessing your logistics costs can benefit your business by:
- Providing clear insight into your spending
- Showing precisely where your money goes
- Facilitating the identification of cost-saving opportunities
4 Strategies to Reduce Logistics Costs
Reducing costs is crucial for a successful logistics strategy. This is especially true as rising costs can impact profitability.
Bringing Delivery In-House
Using a third-party logistics provider (3PL) for deliveries can simplify scheduling and routing but comes at a high cost. Outsourcing means you're subject to the 3PL's pricing changes.
Setting up an in-house delivery team lets you manage costs. It also lets you explore cost-saving strategies like reverse logistics. While there are upfront expenses for hiring drivers and acquiring vehicles, keeping delivery in-house retains profits within your business.
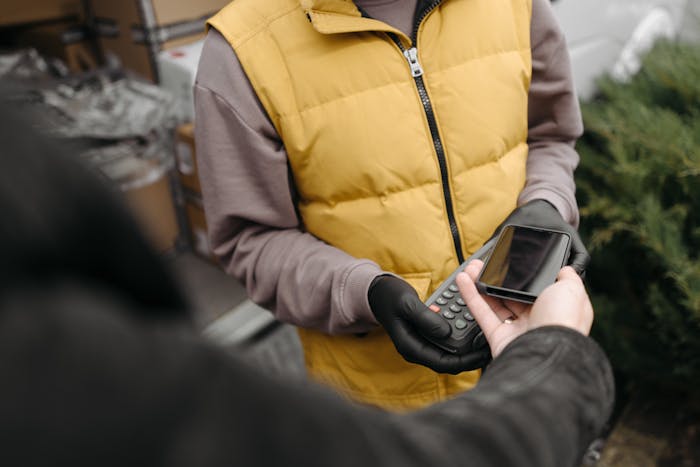
Optimize Last Mile Delivery with Software
Last mile delivery is a costly and critical part of logistics, impacting customer experience the most. Usually, managers or a single dispatcher handle logistics planning and routing. However, this can be time-consuming and prone to errors.
Logistics management software automates this process, saving time and reducing errors. This streamlines delivery planning and ensures a smoother customer experience.

Improve Inventory Management
Managing your inventory efficiently can save on warehousing costs. Yet, reducing inventory too much can lead to delays in fulfilling customer orders and harm your business reputation.
Effective inventory optimization helps determine the right amount of each product to keep in stock for optimal levels. This ensures you have the items you need while minimizing storage costs.
Steps to Optimize Your Inventory:
- Determine average daily sales.
- Record detailed sales data for each product.
- Check order preparation time by shippers.
- Calculate the necessary product quantity to fulfill daily orders.
- Adjust inventory levels to align with standard daily order requirements.
It's important to maintain extra inventory known as safety stock. This ensures that unexpected issues, such as delayed shipments from manufacturers, won't affect your ability to fulfill customer orders.
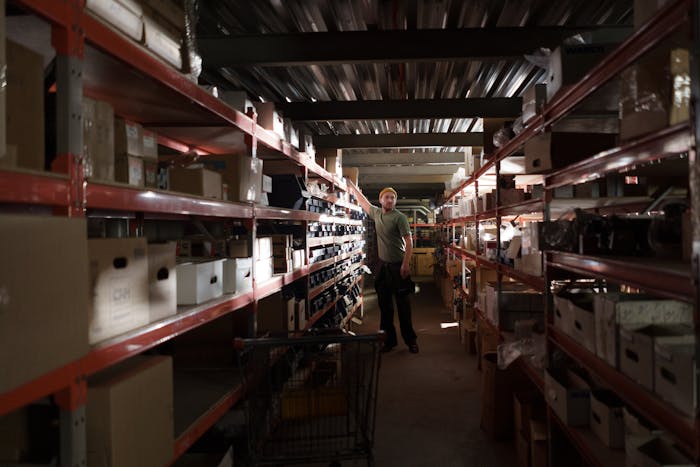
Evaluate Warehouse and Inventory Processes
Regular audits of your warehouse management processes provide insights into workflow efficiency. Assessing inventory levels helps ensure effective management.
Perform these audits monthly or quarterly to track fluctuations, such as seasonal demand changes. This allows for timely adjustments to optimize workflows.
Key Aspects to Assess During Warehouse Audits:
- How shipments of new products are received and managed by your team
- Storage locations within the warehouse and accessibility
- Efficiency of product retrieval for order preparation
- Average staffing levels in the warehouse
Enhance Your Logistics Operations with eLogii
Managing supply chain logistics can be complex, with many components to coordinate. Lowering costs can be especially challenging. Fortunately, you don’t have to tackle everything alone. Leveraging software such as eLogii simplifies logistics planning by automating and optimizing the process. The platform can assist with critical logistics functions, such as:
- Customizable weekly and daily planning
- Creating effective routes while meeting deadlines
- Monitoring purchase orders and deliveries
- Sending delivery notifications and updates to customers
- Creating driver schedules
- Driver mobile app
- Producing performance reports
- Comprehensive training and support for new eLogii users
eLogii also reduces costs by optimizing routes to cut overall mileage. This lowers fuel expenses and extends the lifespan of delivery vehicles by using them more efficiently.

FAQs on Logistics Costs
Here are answers to three frequently asked questions about logistics costs:
What is the largest cost in logistics?
Delivery and transportation costs represent the most significant expense in logistics, with last-mile delivery making up 50% of total shipping costs.
How do you determine logistics costs?
Categorize your expenses into warehousing, transportation, labor, and equipment. Record the precise cost of each expense in these categories. Then, sum up the costs within each category. Finally, combine the costs of all four categories to calculate your overall logistics expenses.
Why is logistics expensive?
Global supply chains are grappling with material shortages, labor shortages, and limited warehouse space. These shortages drive up prices, leading to increased logistics costs across industries.