Inventory shrinkage is figuring out how much of your stuff has gone missing.
You take what you should have and subtract what you have.
The difference is your shrinkage. This matters because your inventory is valuable stuff that helps your business run.
No matter what you sell—hats, veggies, or tech stuff—your inventory is valuable.
When things go missing, it's bad news.
Whether it's because of sneaky vendors, sticky-fingered employees, or just counting mistakes, you're losing money.
You put cash into getting or making your stuff; if you can't sell it, that's cash down the drain.
According to Fortune, the retail industry is experiencing a $100 billion ‘shrink’ crisis.
Of course, you don't want your inventory mix-ups adding to this problem.
We'll cover what inventory shrinkage means and how to work out the numbers.
Plus, we'll discuss the usual reasons for shrinkage and offer some tips to keep your inventory safe.
Understanding Inventory Shrinkage
Inventory shrinkage occurs when your actual inventory falls short of what your records say you have.
For instance, if your records claim you have 1,000 items in stock but you count and find only 995, that’s shrinkage.
This can be due to paperwork slips.
For example, if the accounting team mistakenly records 1,000 items when there are 995, that's shrinkage.
Shrinkage can also result from operational issues, like damage or loss of inventory.
Inventory shrinkage formula
Calculating your inventory shrinkage isn't rocket science.
Here's the formula:
Inventory Shrinkage Value = Total Value of Inventory Recorded by Accounting - Total Value of Inventory You Have
You can also express this number as a percentage, known as your inventory shrinkage rate.
This makes it easier to compare.
To find this rate, divide your inventory shrinkage value by the actual inventory number, then multiply by 100.
Here's how to find the inventory shrinkage percentage:
Inventory Shrinkage Value / Total Value of Inventory Recorded by Accounting = Inventory Shrinkage Rate x 100 = Inventory Shrinkage Rate Percentage
Example of Inventory Shrinkage
To better understand how inventory shrinkage affects your profits, let's consider a scenario:
Imagine you run an eCommerce store selling knitted hats.
It takes two hours to craft each hat, and you pay your employees $15 per hour, totaling $30 in wages per hat.
Additionally, each hat requires $20 worth of materials.
In total, producing a single hat amounts to $50.
Your warehouse stocks 100 hats, valuing the inventory at $5,000 ($50 per hat multiplied by 100).
Yet, suppose a moth infestation damages ten hats, rendering them unsellable.
Though your inventory accounts state 100 hats in storage, the actual count reveals only 90 hats remaining.
To find your inventory shrinkage value, subtract the total value of the inventory you have from the total value recorded by your accounting department.
This gives you insight into the discrepancy between your records and reality.
In essence:
With $5,000 representing the total value of 100 hats ($50 per hat), and $4,500 reflecting the value of 90 hats ($50 per hat),
The difference of $500 reveals the Inventory Shrinkage Value,
Signifying $500 worth of hats that cannot be sold to customers.
So, how does this impact your profits?
Let's break it down:
When you sell each hat for $60, your profit per hat amounts to $10. This profit is calculated by subtracting the production cost of $50 from the sales price of $60.
With a full warehouse of 100 hats, you'd earn $1,000 in profits ($10 profit per hat x 100 hats sold).
Yet, with only 90 hats in stock, your potential profits drop to $900 ($10 profit per hat x 90 hats sold).
That moth infestation has essentially cost you $100 in potential profits!
Certainly! Here's how you can calculate the inventory shrinkage rate percentage using the example:
Divide the inventory shrinkage value ($500) by the total value of inventory recorded by accounting ($5,000).
So, 5005000=0.105000500=0.10.
Then, multiply by 100 to get the percentage: 0.10×100=10%0.10×100=10%.
Thus, the inventory shrinkage rate in this example is 10%.
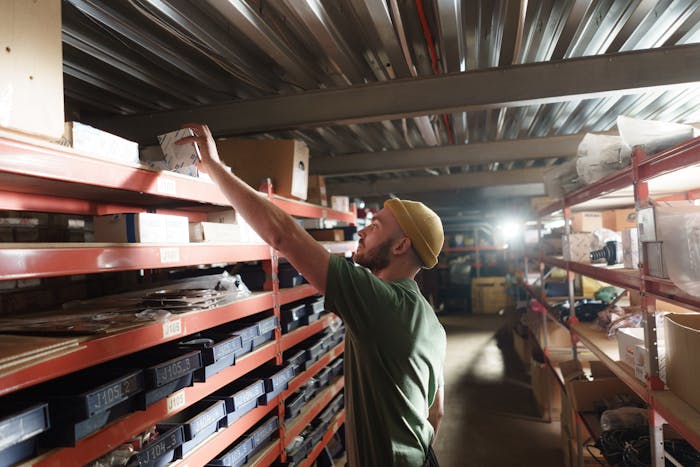
Reasons for Inventory Shrinkage
As evident, inventory shrinkage can result in financial losses. To safeguard your finances, it's crucial to take proactive measures to prevent it.
Here are some reasons why inventory shrinkage might happen:
- Theft. Unfortunately, some inventory can go missing due to theft. This could be employees taking items from the warehouse or shoplifters snatching products from the shelves.
- Supplier issues. Sometimes, suppliers might not deliver the full amount of inventory that was ordered or paid for. This can happen if you rely on external suppliers for your products.
- Damage or spoilage. Accidents can happen, leading to damage or spoilage of inventory. For example, flooding could ruin products, or an employee might accidentally drop and damage items.
- Mistakes. Human errors, like counting mistakes in the inventory records, can also contribute to shrinkage. This might occur in the accounting department, for instance.
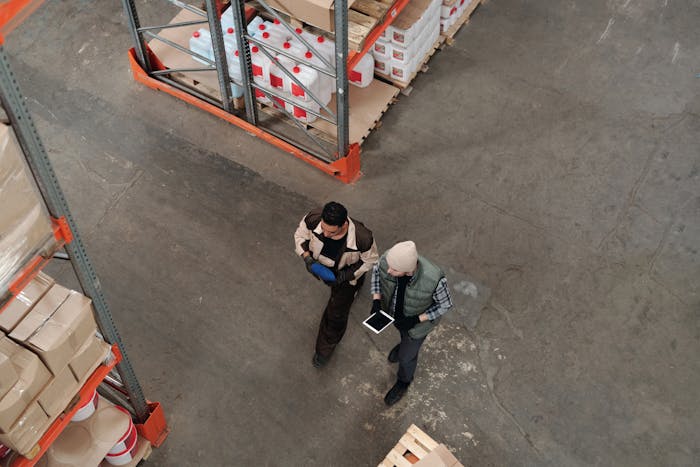
Ways to Avoid Inventory Shrinkage
Now that you're aware of the typical reasons behind inventory shrinkage, you might be curious about how to stop it from happening.
Here's a brief overview of strategies to minimize the chance of inventory shrinkage:
- Track your inventory closely. Utilizing digital barcode systems that track items at every stage of the supply chain can deter employee theft. For instance, requiring delivery personnel to scan each product can discourage theft, as they're individually accountable. Inventory tracking is part of enhancing material handling, which focuses on the efficient movement, storage, and safeguarding of goods throughout the supply chain.
- Conduct routine physical inventory checks. It's essential to count inventory at key stages, such as upon receipt from a vendor, to mitigate the risk of supplier fraud. Regularly verify your inventory counts. Establish a consistent schedule, whether it's daily or weekly. Additionally, diversify inventory responsibilities among many staff members to prevent errors or potential theft resulting from sole accountability.
- Enhance your security measures. Put in place trackable barcodes for added security. Also, consider locking up valuable inventory accessible only by authorized personnel. For physical stores, install security systems such as shoplifting alarms and CCTV cameras to deter theft.
- Ensure product protection. Store inventory in a secure, dry location to prevent damage. Secure shelving units to prevent items from falling. Additionally, invest in proper packaging for shipping to safeguard products during transit and ensure safe delivery to customers.
- Use inventory management tools. These help to track inventory levels during each cycle count. Cycle counting involves physically counting inventory, whether daily or monthly, to ensure alignment with recorded levels. This practice also enhances capacity planning, aiding in meeting supply chain demand. For instance, use inventory management software to automate reorders when inventory levels run low.
- Consider outsourcing your inventory management to a third-party fulfillment company. These professionals handle tasks such as storing, counting, and tracking inventory. They also fulfill orders by picking, packing, and shipping items on your behalf. Using specialized software, they track inventory and provide detailed reports on levels, simplifying the detection and management of shrinkage.
Track Your Inventory Throughout the Supply Chain
Inventory shrinkage occurs when the quantity of inventory on hand doesn't align with the recorded amount in your accounting records.
Tracking inventory shrinkage is crucial because inventory loss can lead to financial losses, impacting your business's profitability.
Regularly calculating inventory shrinkage enables prompt detection and investigation of potential causes.
Various factors, such as damage, theft, and administrative mistakes, can contribute to shrinkage.
Understanding the root causes of inventory shrinkage allows you to implement strategies like enhancing warehouse security and improving inventory tracking to mitigate its impact.
You should safeguard your inventory during the last-mile delivery process, the order fulfillment process when products move from the warehouse to the customer.
Simple measures such as using sturdy packaging and ensuring correct shipping labels and forms can enhance the safety of packages en route to customers.
If you operate a shipping or retail business and oversee your last-mile delivery, a solution like eLogii can be beneficial.
eLogii enables real-time tracking of deliveries, ensuring you always have visibility into the whereabouts of your inventory during transit.
Moreover, eLogii offers cost-saving benefits. Its route optimization feature determines the most efficient sequence of delivery stops for drivers, helping to cut transportation expenses such as fuel costs.
Additionally, eLogii includes proof-of-delivery functionality and allows you to set delivery time windows. You can also provide customers with live updates on their deliveries.