Efficiently managing work-in-process (WIP) inventory is essential for keeping production smooth. It helps to cut down on costs and improve overall profitability. By keeping a close eye on WIP, you can avoid bottlenecks, reduce waste, and make sure that resources are used effectively. All of this helps make your business more competitive.
In this article, we’ll cover why WIP inventory matters in inventory management, its impact on your bottom line, and a simple way to calculate it. With these insights, you’ll be better equipped to control production flow and improve your business’s performance.

What Is Work-in-Process (WIP) Inventory?
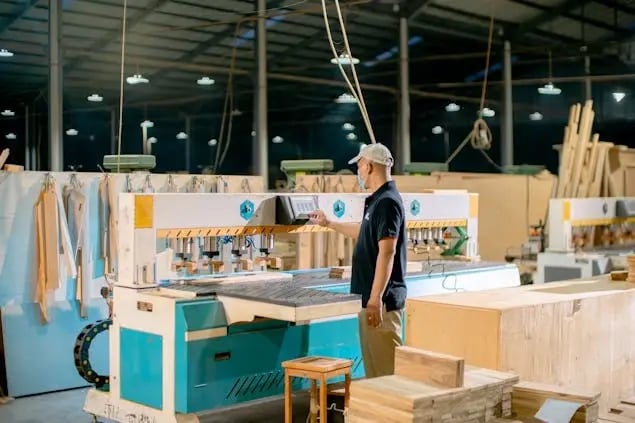
Work-in-process (WIP) inventory includes goods that are still being made and not yet finished. It’s a key part of the supply chain, representing items in progress as they move from raw materials to completed products.
Keeping track of WIP inventory gives you insight into how smoothly your production is running. It helps you make better decisions to improve your supply chain and boost important performance metrics.
For example, imagine a company that makes custom furniture. The WIP inventory would include all the parts being put together but not finished yet. This could be things like wooden pieces waiting to be assembled or chairs with missing legs. Tracking WIP inventory helps spot delays, control production time, and boost overall efficiency.
Reducing or cutting WIP inventory to avoid extra costs is a good idea. Cutting down on it frees up cash, improves how smoothly things run, and helps you better respond to customer needs and market shifts.
Finding the right balance is key to managing working capital and keeping production running without a hitch.
Although "work-in-process inventory" and "work-in-progress inventory" are often used the same way, they have some important differences.
Work-in-process is used mainly in manufacturing and refers to products that are still being made. Work-in-progress, on the other hand, is a broader term. It can apply to any ongoing task or project, like a website under development or a building under construction.
Both terms highlight the need to track and manage work that’s still in progress to stay efficient and productive.
How to Calculate WIP Inventory
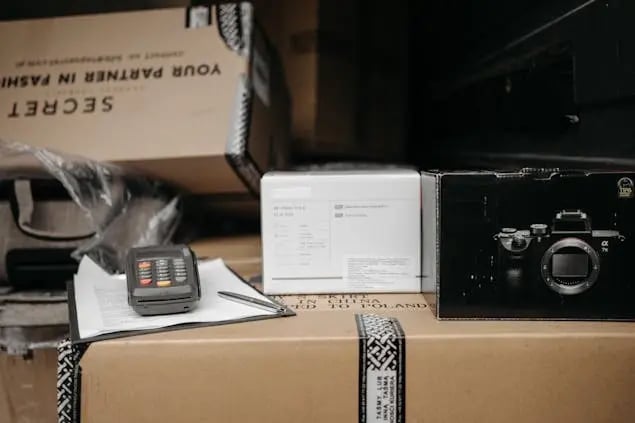
To calculate WIP inventory, you'll need to consider the starting WIP inventory from the previous period, the total manufacturing costs during the current period, and the cost of goods manufactured (COGM). This will give you the ending WIP inventory.
Manufacturing costs include both direct labor and production expenses. The formula for WIP inventory is:
Ending WIP inventory = Beginning WIP inventory + Manufacturing costs - COGM
Let’s go through an example to better understand how to calculate WIP inventory:
Imagine a furniture company that starts the month with $8,000 in WIP inventory. During the month, the company spends $20,000 on manufacturing costs, including materials and labor.
By the end of the month, the company finishes $22,000 worth of furniture, which is transferred to the finished goods inventory. This amount represents the cost of goods manufactured (COGM).
Now, using the WIP inventory formula:
Ending WIP Inventory = ($8,000 + $20,000) - $22,000
Ending WIP Inventory = $6,000
The ending WIP inventory of $6,000 represents the value of items still being made at the end of the month. This figure helps you keep track of production efficiency, how well resources are used, and inventory levels.
By tracking WIP inventory over time, you can spot trends, find possible bottlenecks, and see where there’s room for improvement. This leads to better productivity and cost control throughout the production process.
Benefits of Managing WIP Inventory
Effectively managing WIP inventory can improve key areas like cost control, production planning, decision-making, efficiency, and customer satisfaction.
Let’s look at some of the main benefits that can boost both your operations and your bottom line.
Cost Control
Keeping WIP inventory in check helps you manage overhead costs by avoiding the buildup of unfinished goods.
Reducing excess WIP inventory means you can avoid extra storage and handling costs, lower the risk of items becoming outdated, and free up cash by reducing tied-up resources.
For example, say you notice a delay in packaging that slows down order fulfillment. Fixing this bottleneck allows items to move through production faster, helping avoid costs linked to excess WIP inventory.
Production Planning
Efficient production planning means accurately tracking all inventory, including WIP inventory, raw materials, and finished goods.
Monitoring WIP inventory helps you schedule production better, use resources more efficiently, and manage lead times.
If you notice that WIP inventory is often low, you might adjust your purchasing to keep a steady supply of raw materials.
On the other hand, if WIP inventory is high, it might signal the need to increase production to finish more items or shift resources to resolve any delays.
Better Decision-Making
Tracking WIP inventory helps you make smarter decisions about production, purchasing, and resource use.
For example, by observing WIP inventory trends, you can spot demand changes, like increased sales during holidays, and adjust production schedules or buying strategies to match.
This proactive approach leads to smoother operations and can give you a competitive edge in the market.
Efficiency
Keeping track of WIP inventory is a good way to spot inefficiencies in your production and make improvements.
By fixing delays, streamlining workflows, and adjusting resources when needed, you can reduce lead times and boost productivity.
If WIP inventory is often high, it may be time to add resources or upgrade equipment to work faster and keep WIP levels under control
Customer Satisfaction
Managing WIP inventory well can lead to shorter lead times, better product availability, and happier customers.
With an organized production process and controlled WIP, you can ensure that finished products are ready on time, avoiding delays and improving the customer experience.
Meeting customer expectations and delivering on time strengthens relationships and builds loyalty.
How to Manage WIP Inventory
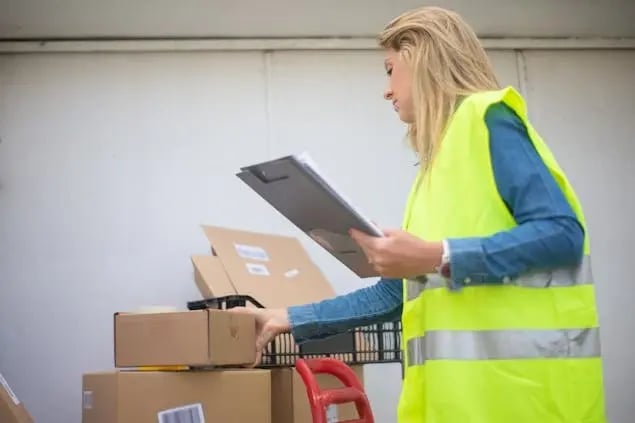
Keeping WIP inventory at the right level is key to better inventory management. Since WIP inventory is listed as a current asset on the company’s balance sheet, managing it well is also important for accurate financial reporting.
Here are some practical steps to help you manage WIP inventory more effectively, boosting both operational efficiency and business performance.
Calculate Cost of Goods Manufactured (COGM)
The first step to managing WIP inventory well is calculating the cost of goods manufactured (COGM).
COGM is the total cost of all goods completed within a certain period, including expenses for direct materials, labor, and production overhead.
Knowing your COGM is essential for WIP management because it shows how much it costs to turn raw materials into finished products. This can help you spot areas where you might save on costs.
For example, if a clothing manufacturer calculates its COGM and sees that fabric costs are high, it might look into negotiating with suppliers or finding more efficient fabric options. This could lower material costs, which, in turn, would reduce the overall COGM.
Calculate Cost of Goods Sold (COGS)
Knowing your cost of goods sold (COGS) is important for managing WIP inventory.
COGS is the total cost of all the products a company makes and sells within a certain period. It includes both material costs and direct labor needed to make the products.
COGS and COGM differ in timing: COGM is the cost of production during a period, while COGS is the cost of goods sold in that same period, including any extra costs to prepare products for sale.
Calculating COGS helps you see your actual production costs and can reveal inefficiencies in your process. Comparing COGS to revenue shows your gross margin, a key measure of financial health.
For example, if a bakery sees a spike in its COGS, it could mean that ingredient costs rose unexpectedly or that resources are being wasted in production. Fixing these issues can reduce COGS and improve profit margins.
Lean Manufacturing Principles
Lean manufacturing principles focus on cutting waste and boosting efficiency in production.
Using these principles can help you manage WIP inventory better. Here are a few key ideas:
- Just-in-Time (JIT) Production. This method involves making goods only when they're needed, which helps avoid excess inventory, including WIP. JIT can reduce the costs of storing and handling WIP inventory. For example, a bakery might use JIT by baking fresh bread only when a customer orders, preventing waste and extra inventory.
- Continuous Improvement (Kaizen): Kaizen is the idea of ongoing improvement, where everyone in the organization works together to refine processes and reduce waste. Applying Kaizen lets you regularly review and improve your production steps, which can lead to less WIP inventory over time.
- Value Stream Mapping. Value stream mapping is about visually laying out each step in the flow of materials and information. This process highlights any waste or areas needing improvement, making it easier to find ways to optimize WIP inventory management.
- Standardized Work. Standardized work creates specific procedures for each person’s tasks in the production process, which reduces variation and keeps things consistent. This helps avoid overproduction and limits excess WIP inventory since every worker follows a clear set of steps.
- 5S Workplace Organization. The 5S method helps create a clean, organized, and efficient workspace that supports smoother workflows and lowers WIP inventory. It follows these five steps: Sort, Set in Order, Shine, Standardize, and Sustain.
- Kanban. Kanban is a scheduling tool used in lean manufacturing and JIT production. It uses visual signals to manage production, helping ensure that only what’s needed is produced, which minimizes WIP inventory.
Boost Your Bottom Line with WIP Inventory Management
Getting a handle on WIP inventory management can make a big difference in controlling costs, planning production efficiently, making smart decisions, and keeping customers happy. By streamlining your processes, you can spot bottlenecks and cut down on extra inventory.
eLogii can support these efforts by optimizing your last-mile delivery, offering features like route planning and real-time driver tracking to improve your overall inventory flow.
