Cold chain logistics are really specialized and can be tricky. No matter how big or small your business is, getting it right is tough, so business owners need to do their homework to set up their own cold chain processes.
The way COVID-19 vaccines have been distributed has made people everywhere think more about cold chain logistics. Over a billion vaccine doses have been given out around the world. Yet, the distribution has had a lot of problems, like unused vaccines and storage issues. Namely, according to a recent POLITICO analysis. €4 billion vaccines have been thrown away. Problems aren't just with vaccines; they're common in cold chain transport in general.
In this article, we will explore what cold chain logistics entails, the typical challenges it encounters, and six effective methods for managing products that require cold chain transportation. Understanding cold chain logistics is key to overcoming these challenges and ensuring efficient delivery.

What is Cold Chain Logistics?
Cold chain logistics involves transporting and distributing products that are sensitive to temperature. It is commonly used in industries such as food, agriculture, healthcare, and pharmaceuticals. Cold chain logistics ensures that perishable items are transported with temperature controls throughout storage and transit. Knowing how a cold chain works is essential for businesses to maintain the quality and safety of temperature-sensitive products.
For instance, meat products like chicken and fish must be stored at temperatures below freezing to maintain their quality. Low temperature logistics ensures the integrity of temperature-sensitive shipments, such as meats and vegetables, throughout their supply chains.
Why Cold Chain Logistics Matters
Cold chain logistic management is crucial for several reasons:
Product Quality Preservation
Maintaining product quality during transport and storage is key to a smooth supply chain. Cold transportation logistics ensures that perishable items like food and medicine stay safe and effective for use. By monitoring transportation conditions in real time, businesses can meet customer expectations and comply with industry standards.
Regulatory Compliance
Industries like food and pharmaceuticals must follow strict rules for transporting temperature-sensitive products. Proper logistics management helps businesses stay compliant, avoid legal issues, and build trust with customers. This helps ensure long-term success.
Customer Satisfaction
Delivering quality products consistently leads to happier customers and stronger loyalty. A well-managed cold chain reduces product loss, damagfe, and returns, ensuring customers receive fresh and safe items. Efficient cold chain practices not only boost customer trust but also improve your business's environmental and financial performance.
What Does Cold Chain Logistics Involve?
Cold chain logistics is like any logistics process where a product is moved from one place to another.
What makes cold chain transport special is the need to keep products at specific temperatures, or the conditional demand. Also, maintaining load integrity and transport integrity using technology during transport is important. Let’s break these terms down:
Conditional Demand
The arrival time and condition of products create the demand for cold chain shipping.
For example, fresh produce like apples need to be kept between -1°C and +4°C. Even at 4°C, they spoil four times faster than at 0°C. So, if apples are shipped even a bit warmer than they should be, they might not be in good condition when they get to the grocery store. That affects whether the store will sell them.
Hospitals often order medicines only when they need them to avoid costs and spoilage. This means pharmaceutical wholesalers and distributors must prioritize these orders. Pharmacies give patients estimated times for when they can get their medicines, and if they don't get them in time, patients might go to another pharmacy next time, reducing future orders from that distributor.
Load Integrity
Load integrity is about the technology needed to keep products in good condition during shipment. This includes how products are packed and what cooling materials are used.
These technologies include blast freezers, insulated containers, vacuum packing, and perforated plastic containers or boxes. Reefer containers are also part of this because they keep the load at the right temperature during transport.
Transport Integrity
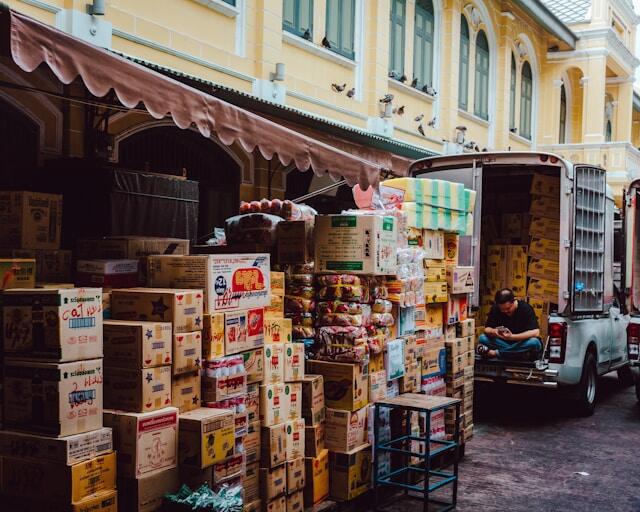
Transport integrity is the technology needed to maintain a temperature-controlled environment throughout the cold chain.
Examples include temperature sensors and monitors in trucks. Also, smart packaging solutions provide accurate data on the temperature throughout the shipment.
When building your cold chain logistics process, start with your product. Ask yourself:
- What temperature does my product need to stay at for the best quality?
- What technologies do I need to keep my product at this temperature from start to finish?
- How can I track the temperature to ensure the product stays in good condition during transport?
Common Challenges in Cold Chain Logistics
Cold chain logistics is tough because keeping products at the right temperature during transit is difficult.
Poor Airflow
Airflow means how air moves around products in a refrigerated space. Good airflow keeps the temperature even in freezers, trucks, and trailers, ensuring product quality. Bad airflow an disrupt cold chain fleet management by causing problems like short-cycling, top-freezing, and hot spots.
Short-cycling happens when cold air can't travel through the entire storage or transportation unit. For instance, if pallets are stacked from the floor to the ceiling of a truck, the cold air won't be able to move from the cooling unit to the back of the truck, making the temperature uneven.
Top-freezing happens when products are placed too close to the cooling air, causing frost damage.
Hot spots occur when the temperature isn't consistent throughout the shipment, causing some parts to be warmer or cooler than others.
Temperature Fluctuations
.jpg?width=640&height=390&name=ibrahim-boran-pV5arhEZHiA-unsplash%20(1).jpg)
A temperature fluctuation occurs when a product is exposed to temperatures outside its recommended storage range.
These fluctuations can happen at any point in the cold chain process, from the start to the end. They can be caused by various factors, such as technical issues with storage or transport units, power outages in storage facilities, or inspections during border crossings.
For pharmaceuticals, temperature fluctuations can lead to product loss. If, for instance, products are accidentally exposed to freezing temperatures during transport of the shipments have to be recalled.
Six Best Practices for Cold Chain Transport Management
Managing your cold chain effectively revolves around ensuring your products remain at the correct temperature. These practices will help you achieve that objective.
1. Prioritize Delivery Orders
When transporting products that are sensitive to both time and temperature, it's crucial to prioritize the sequence of your deliveries to ensure you meet all customer needs.
Setting delivery priorities with eLogii is straightforward. When you upload your orders into eLogii, you can assign a high priority to tasks, making them more important than others. Or, you can adjust task priorities after they're created by navigating to Tasks ⇒ Task Profile ⇒ Task Priority. Even more so, you can assign a priority level from 1 to 100, with 1 being the lowest and 100 the highest.
Once your orders are uploaded, you can benefit from team-based planning and optimization. Tasks assigned to specific teams allow for optimized route planning. Users can perform optimizations for single-day or multi-day routes respectively, based on date ranges.
2. Choose the Right Vehicle and Equipment
Selecting the right packaging system is crucial when it comes to maintaining cold chain during transport.
You have two main options: active and passive packaging systems. Active systems regulate your product’s temperature actively, using tools like refrigeration units such as blast freezers and reefer trucks. Passive systems, on the other hand, maintain temperature without active regulation, using materials like dry ice, gel packs, and plastic coolers.
Many cold chain systems use a combination of both active and passive systems. The choice between them depends on the size of your cold chain operation, the nature of your products, shipping destinations, and customer expectations.
3. Conduct Pre-Trip Inspections
Before transporting your products in the cold chain process, it's essential that drivers perform thorough pre-trip inspections of both the products and vehicles.
Here is a useful checklist for conducting pre-trip inspections:
- Ensure the refrigeration unit is operating smoothly.
- Verify there is sufficient diesel fuel for the journey.
- Check the load temperature before loading.
- Pre-cool the truck to eliminate residual heat.
- Perform a defrost half an hour after loading to clear the evaporator coil for optimal cooling performance.
- Inspect the truck for any leaks in the refrigerated air.
- Check for condensation on the body when loaded to detect potential damage or insulation gaps.
- Verify that doors are tightly sealed.
4. Maintain Optimal Airflow for Your Products
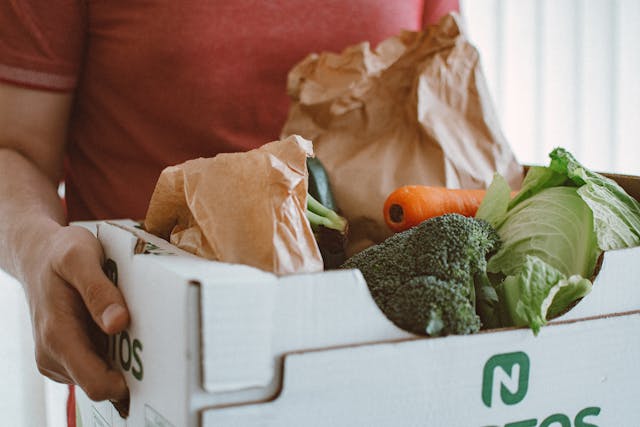
As previously mentioned, poor airflow can damage products during transportation. Here are some ways to minimize the risk of poor airflow affecting your products:
- Reduce the frequency of opening refrigeration unit doors.
- Ensure loads are properly packaged to allow for optimal airflow.
- Stack loads on pallets to avoid blocking air passages.
- Keep the transport unit floor clear of obstructions and debris to maintain proper air circulation.
5. Perform Regular Maintenance for Your Cold Chain Fleet
It's crucial to regularly inspect refrigeration units to avoid breakdowns during operations.
Depending on the value of your products, you could be carrying anywhere from $5,000 to $50,000 worth of inventory on a single trip. Regular vehicle maintenance is preferable to facing a breakdown that could significantly impact small business logistics.
6. Offer Real-Time Updates to Your Customers
Providing real-time tracking information to customers helps them stay informed about their shipments, especially for time-sensitive orders.
With eLogii, you can share real-time order tracking via text and email. Customize the tracking branding and messaging so customers know the information is coming from your company.
Streamline Your Cold Chain Logistics Using eLogii
%20(1).webp?width=635&height=353&name=elogiisoftware%20(2)%20(1).webp)
Effective supply chain management relies on a well-organized logistics process. This ensures parts, products, and services move smoothly from suppliers to the end user.
Deliveries must arrive on time and in good condition. The purpose of logistics operations is to improve efficiency, lower costs, and enhance service quality.
Although managing quality cold chain logistics can be challenging and intricate, it doesn’t have to be.
eLogii's route optimization software streamlines your cold chain logistics management, making it easier to dispatch your temperature-sensitive shipments.
Namely, eLogii simplifies cold chain logistics by optimizing delivery routes and prioritizing time-sensitive shipments to reduce spoilage risks.
Its real-time tracking and fleet management features ensure proper temperature control, load integrity, and seamless delivery operations.
The platform also supports pre-trip inspections and provides real-time updates to customers, enhancing trust and transparency.
By streamlining these processes, eLogii helps businesses maintain product quality and improve the efficiency of their cold chain operations.
