If you're reading this, you might wonder: What's maintenance management, and why does it matter?
In business, sudden equipment failures can be a significant problem, especially when they involve crucial equipment.
Studies show that a significant part of unplanned downtime is caused by aging equipment and unexpected mechanical issues.
Maintenance management is crucial for avoiding these problems by ensuring regular maintenance. It can also help extend the lifespan of older equipment until it's time for a replacement.
Let's delve into what maintenance management entails, which businesses use it, and ways to enhance it within your company.
To access the section that interests you most, simply click on the link below:
Maintenance Management: Explained
Maintenance management means planning, scheduling, and overseeing upkeep for important equipment like vehicles and machinery.
It involves predicting problems and setting up regular maintenance to stop them.
For example, you might schedule oil changes and checkups for your trucks. More advanced methods might use technology to predict which parts need replacing.
Using current data helps you improve maintenance and save money.
But there are other big reasons why maintenance management matters for businesses.
The Importance of Maintenance Management
Maintenance management is crucial for keeping operations running smoothly and avoiding unexpected disruptions.
Without proper monitoring, equipment breakdowns can cause significant problems. These problems could be delays in production or shipping, damaged goods, and lost revenue.
Following a maintenance plan not only saves money but also helps ensure compliance with regulations, preventing costly fines.
The benefits of maintenance management vary depending on the chosen approach.
Different Approaches to Maintenance Management
Various strategies exist for maintenance management, such as preventive, reactive, predictive, and others.
Now, let's examine the advantages and disadvantages of each approach.
Reactive maintenance
Reactive maintenance, also known as breakdown maintenance, is common among small businesses. Essentially, you wait until the equipment breaks down before taking action.
However, this approach can lead to unexpected downtime and increased costs. Overall, it's not a wise strategy.
Scheduled Maintenance
Regularly schedule maintenance tasks based on time or usage metrics such as mileage. For example, changing oil every 6 months or after driving 5,000 miles is an instance of this approach. It's easy to implement and can prevent unnecessary breakdowns and repairs. However, it may result in spending time and money on equipment that doesn't need immediate attention. Additionally, heavily used equipment might not receive adequate maintenance.
Predictive Maintenance
Track equipment condition and performance in real-time to schedule servicing and prevent downtime. This method helps in keeping maintenance costs low while ensuring continuous business operations. Apart from predicting issues, many companies also perform some preventive maintenance tasks like lubrication or oil changes.
Usage-Based Maintenance
Usage-based maintenance assesses equipment usage metrics to predict and schedule the next service. It goes beyond preventive maintenance but is not fully predictive. It could track metrics like miles driven or products handled, tailored to each business. It's cost-effective compared to full predictive analytics, offering similar benefits. It is especially beneficial for transportation-related maintenance, where many fleet managers already have the necessary functionality.
Reliability-Centered Maintenance
Reliability-centered maintenance involves identifying and prioritizing critical processes within a company and then adjusting maintenance operations accordingly. It often combines preventive and predictive maintenance techniques to achieve maintenance goals. This approach is effective in improving core maintenance Key Performance Indicators (KPIs) and reducing unscheduled downtime.
The Most Common Maintenance Approach
From 2019 to 2021, for example, the most common maintenance approach was preventive maintenance. The majority of companies adopted it. It's the simplest type of maintenance program to establish.
Regular tasks like lubrication, oil changes, and replacing worn parts with new ones are straightforward. It's the easiest method for ensuring effective maintenance.
Of course, enhancing the decision-making of maintenance managers can be achieved by investing in Predictive maintenance (PdM) or Computerized Maintenance Management Systems (CMMS).
Who Requires Maintenance Management?
Various companies across industries depend on maintenance management to ensure smooth business operations.
Let's take a closer look.
Field Service and Maintenance Enterprises
For businesses providing maintenance services to clients, having an efficient maintenance management system is crucial.
From managing work orders to anticipating and averting issues, a structured process is essential. Manual approaches often result in confusion and poor decision-making.
Logistics, Distribution, and Delivery Services
Effective maintenance management is essential for optimizing private fleets. Without it, vehicles may unexpectedly break down, causing delays or damaging sensitive goods like food. Neglecting lightly-used vehicles can result in unnecessary expenses.
HVAC Installation, Repair, and Maintenance Firms
HVAC companies rely on data-driven maintenance programs to ensure customer satisfaction. Preventing AC breakdowns shortly after installation is critical for maintaining a positive reputation. A robust program can also secure ongoing revenue beyond initial installation fees.
Pool Maintenance Services
In the pool maintenance sector, efficient maintenance programs are vital for ensuring pool safety and cleanliness. Without them, risks such as algae growth and pump failures can jeopardize client satisfaction and retention.
Do You Need CMMS Software for Maintenance Management?
For small businesses and maintenance teams, it's not necessary to use a dedicated solution.
You can get most of the benefits with preventive or usage-based maintenance. That requires less initial investment.
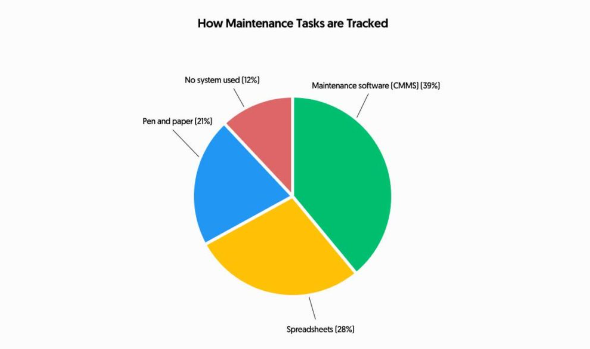
While maintenance management software can be challenging to set up, it's not as expensive as it used to be. Some new SaaS companies offer plans starting at just $33 per month.
Yet, the main issue is learning how to use the new system and creating custom APIs for important analytical functions.
Enhance Maintenance Program Efficiency with eLogii
Transitioning from spreadsheets to eLogii is a cost-effective and straightforward method. It will help to increase the productivity of your maintenance teams.
1. Enhance the effectiveness of your maintenance technicians
Route optimization eliminates the need for manually connecting dots on Google Maps. You can simply import tasks in bulk.
You can do so using a CSV file by going to Tasks and selecting Import Tasks.
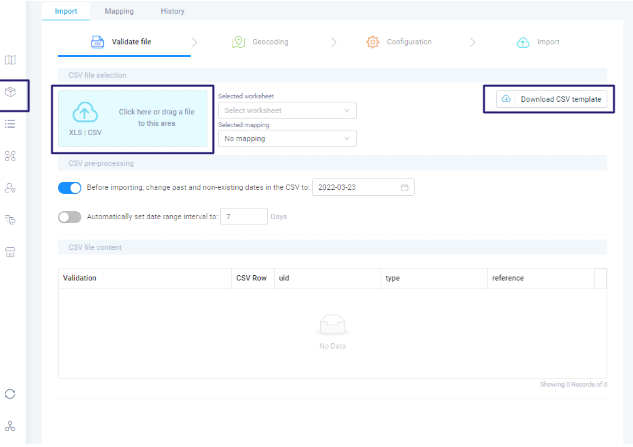
When assigning tasks to technicians, use the "Teams" column in your CSV file. Specify either the UID or the name of the team.
If you need to assign tasks to many teams, separate their names with a comma, for example, "Team 1, Team 2".
Implementing our advanced features can greatly improve internal workflows, providing immediate benefits.
By accelerating scheduling and optimizing routes, the capacity to manage maintenance work orders can be doubled.
2. Cut Unsuccessful Maintenance Assignments
Handing over maintenance scheduling to an automated system may raise concerns. However, eLogii is purposefully crafted to tackle real-world complexities efficiently.
For instance, it ensures the right technician with suitable qualifications and tools is assigned to each specific task.
It also considers factors like time windows, deadlines, and task priority when generating routes and schedules.
Rest assured, our software prioritizes managerial control, allowing supervisors to review and adjust plans manually. This approach significantly expedites the process without sacrificing oversight.
3. Enhance Customer Satisfaction and Cut Missed Appointments
For field service companies, missed service appointments are a major inconvenience. When customers are unavailable or occupied, rescheduling becomes necessary.
It's a logistical challenge.
Providing precise live estimated time of arrival (ETA) updates via text messages or email notifications to customers offers an ideal solution.
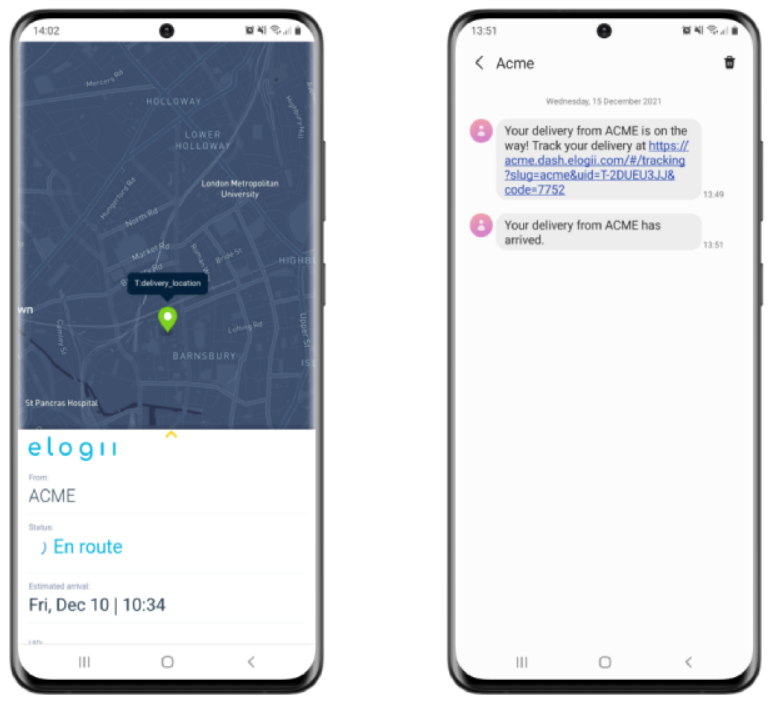
Conclusion
Enhancing your maintenance program doesn't have to be daunting.
There's no need to complicate matters or invest heavily in costly CMMS solutions.
With eLogii, you can efficiently schedule and distribute work orders while simultaneously planning routes for each assignment.
